Have you ever considered pre-provisioning your wireless network?
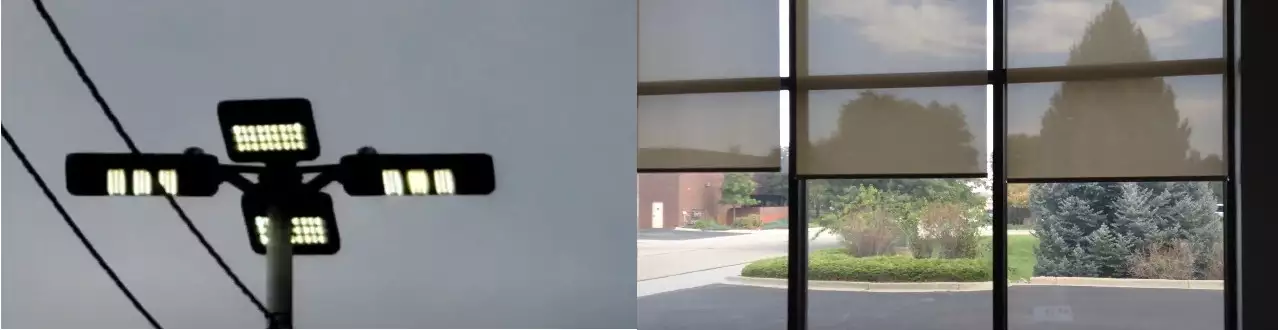
What do you mean, “PRE” provisioning?
Wireless IoT networks can consist of a lot of devices. Even if the initial setup of these devices is easy, it may still be time consuming to perform the setup since there are so many devices. Often, the end customer has little to no experience in setting up a system like this. As with anything, the first time is often confusing and can be difficult.
Let’s take the example of an outdoor lighting system. There may be 20-100 devices that need to be paired to a controller, each put into a zone, and each zone setup with a schedule. The devices will also need to be named something useful, so that when a device fails, it is easy to figure out which physical device it is. All of the software configuration can be done by the end user on site, OR this can be done before the order is shipped to the customer (“pre-commissioning”).
It is just too DIFFICULT…or is it?
The most common argument against pre-provisioning a wireless network is that the cost to do the pre-provisioning is too high to make it worthwhile. The pre-provisioning needs to be done by a knowledgeable person, who is good at it, and their time is valuable. This is not the right way to look at the value of pre-provisioning.
Instead of looking at the COST of pre-provisioning, look at the cost of NOT pre-provisioning. Here are the benefits to pre-provisioning a wireless IoT system:
1.) The installations will be FASTER and therefore lower cost due to the system arriving with minimal time spent on software configuration
2.) There’s a much higher chance of the system working out-of-box since most activities consist of physical ones like installing hardware
3.) Both 1 and 2 will mean LESS support calls. Support Engineers cost money.
4.) Documenting the pre-provisioned system can reduce support calls and time since the installers know how the system is supposed to be set-up…this speeds-up the process and saves money.
Prior to leaving a factory or warehouse, many devices are pre-tested, paired to a controller, then unpaired, and packed for future shipment. Instead, pairing, configuring, and testing the system as needed for a specific installation, can be about the same amount of work as the normal process.
It’s not all Unicorns and Rainbows
Pre-provisioning does have some limitations:
- To do it correctly you need some information from the customer (which lights/shades in each zone, schedules, Etc.). Sometimes this can be hard to get.
- Sometimes devices ship from different places, which means a pre-provisioning step will have to get all the devices to the same location. This can add time and shipping costs.
- If a hardware defect is discovered in a device during the process it will need to be replaced, which means there will need to be replacement units at the place that pre-provisioning is done.
- Pre-provisioning counts against COGS, which may be an accounting battle with the VP-Operations.
Conclusion
Pre-provisioning makes the user experience better, makes the install go faster and smoother and reduces the support calls and the duration of support calls. However, the VP-Operations doesn’t want to further burden COGS. Now what?
The group that benefits the most from pre-provisioning is the support team. The customer experience is better, there are less support calls, and the support calls take less time. So, we make this work by having the support team perform the pre-provisioning and assign this and any associated costs, like extra shipping, to their department. Operations is happy with lower COGS, support realizes greater efficiencies and reduced field problems, and customers benefit by the faster installations.
In our next post we will discuss the trade-offs between
pre-commissioning at factory and in-field commissioning of wireless
devices, and how the two can work together.